1. 서 론
2. 예방적 유지보수공법
2.1 예방적 유지보수
2.2 예방적 유지보수의 필요성
2.3 국내·외 예방적 유지보수 공법 사례
3. 에폭시 박층 포장
3.1 개요
3.2 재료
3.3 실험
4. 결 론
1. 서 론
국토교통부 도로현황조서(Ministry of Land, Infrastructure, and Transport, 2020)에 따르면 2000년 이후 시멘트 콘크리트 포장 연장은 지속적으로 증가하여 고속도로(1차로) 연장의 약 65.63%(12,956 km)에 해당되나, 노후화가 진행되어 리모델링 중장기 계획이 필요하고, 리모델링 대상이 무려 19.51%(2,528 km)에 해당된다. 시멘트 콘크리트 포장 노후화의 증가는 필연적으로 유지보수 예산의 증가로 이어진다. Fig. 1은 한국도로공사에서 2019년 노후 콘크리트 교면포장 증가에 따른 필요예산을 산정한 결과이다. 2016년에 168억 원 규모이던 고속도로 유지보수 예산이 2028년에는 2,757억 원 규모로 무려 16.4배나 증가할 것으로 예측되었다(Korea Expressway Corporation, 2019). 노후 콘크리트 교면포장 증가에 따른 효과적인 유지보수 방안 마련이 시급한 실정이다. 효과적인 유지보수란 예방이 가능한 유지보수로서, 부분적 단면보수의 한계를 극복하고, 기존 노후 시멘트 콘크리트 포장의 수명을 연장하고, 내구성을 확보할 수 있는 공법을 말한다. 콘크리트 포장에 적용 가능한 예방적 유지보수 공법은 기술적인 면에서 시공이 용이하면서 구조적 성능이 확보되어야 하고, 재료적 측면에서는 환경 유해요소를 포함하지 않는 환경친화적인 재료를 사용하는 것이다. 아울러, 공기의 단축 및 공사 중 발생하는 환경 훼손의 최소화, 환경 훼손영역의 신속한 복구 등이 수반된다면 더욱 친환경적인 기술이 될 것이다. 국내 교면포장의 보수방식을 살펴보면 대부분의 유지보수가 사후 개량방식으로서, 균열 및 열화와 같은 손상이 발생하면 손상의 크기와 종류에 따라 적절한 유지보수 공법을 체택하여 적용하고 있다. 연구사례로 2020년 노후아스팔트 및 콘크리트포장의 고마찰 표면처리 공법 바인더 및 골재시방에 관한 조사연구(Jang et al., 2020) 및 2021년 박층 에폭시 덧씌우기 포장의 부착성능과 미끄럼 저항 현장시험에 대한 연구가 실시되었다(Choi et al., 2021).
본 연구의 목적은 노후 된 콘크리트 교면포장 및 노출 교면포장을 보수하기 위한 예방적 유지관리를 위한 에폭시 박층포장 재료의 품질 성능 검토를 통하여 콘크리트계 교면 포장의 노후화로 인한 급격한 손상을 미연에 방지하고자 하는데 있다.
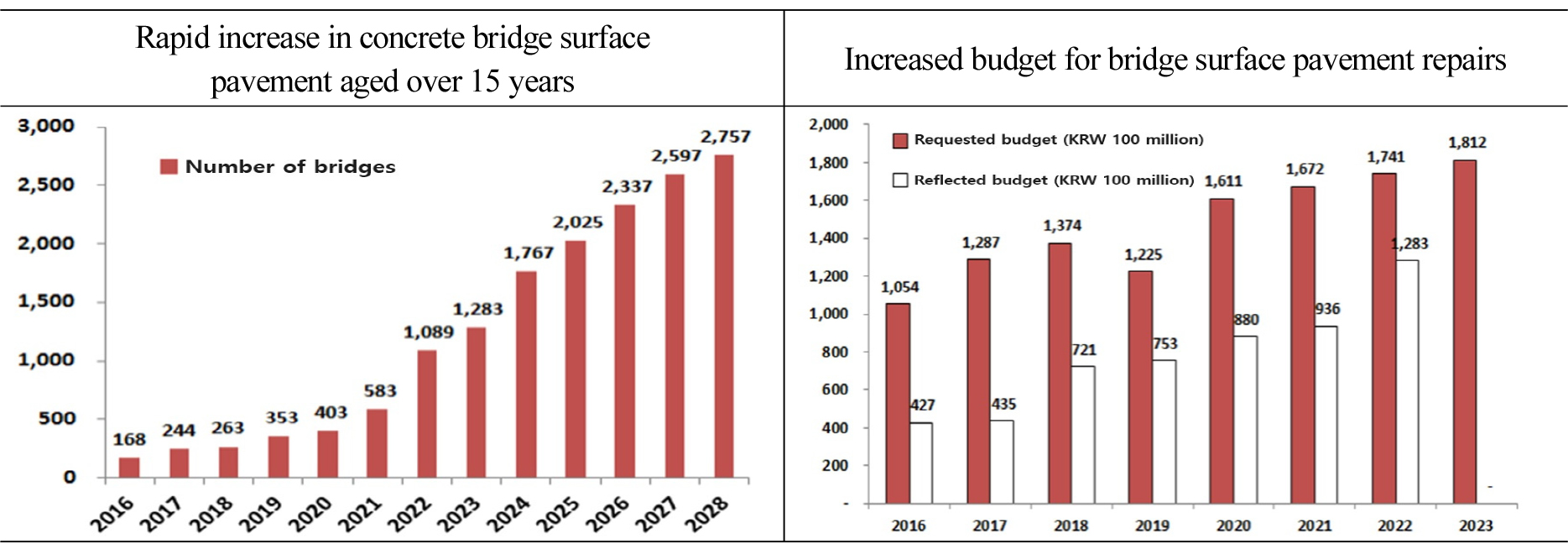
Fig. 1.
Required budget due to increase in aged concrete bridge surface pavement (Korea Expressway Corporation, 2019)
2. 예방적 유지보수공법
2.1 예방적 유지보수
예방적 유지보수는 기존의 도로를 구조적인 능력의 보강없이 도로에서 추후 발생할 파손을 지연시키고 도로의 기능을 유지 또는 향상시키며, 도로를 보존하는데 비용·효율적인 처리공법을 계획된 전략에 따라 시행하는 것으로 정의된다(FHWA, 1998). 즉, 예방적 유지보수는 공용성능이 종료되는 시점에 실시하는 기존의 아스팔트 포장도로의 보수공법과 달리 일상적 유지보수를 통하여 포장도로의 공용성능을 일정하게 유지하여 공용수명을 증가시키는 것이다(Kim et al., 2011)
2.2 예방적 유지보수의 필요성
콘크리트계 교면포장은 교량에서 발생하는 수축팽창 및 차량하중에 의한 진동 흡수와 방수층을 형성하여 우수의 침투로부터 구조물을 보호하고, 평탄성 및 미끄럼 방지 기능, 주행성, 쾌적성 등을 제공하여 주행차량의 안전을 도모하는 역할을 한다. 콘크리트계 교면포장은 차량하중 작용에 의한 진동, 온도변화에 따른 수축팽창 등 다양한 요인에 의해 균열(Crack)이 발생된다. 균열을 통하여 물과 염분을 포함한 유해물질이 기존 콘크리트 슬래브로 침투하여 콘크리트의 열화(Deterioration) 및 철근부식을 유도하여 교량의 내구수명에 영향을 미친다. 이상의 문제점에 대한 현장사진은 Fig. 2와 같다.
또한, 장기간 공용된 콘크리트계 교면포장은 차량운행으로 인하여 콘크리트 표면에 마모가 발생하여 미끄럼 저항성을 상실하게 되고, 우천 시 및 동절기에 도로살얼음(Black ice)이 발생할 경우 미끄럼 저항성 약화로 운전자의 교통안전에 심각한 위험을 초래할 뿐만아니라 보수 지연으로 인한 교면포장 파손 및 교량바닥판 슬래브의 열화가 가속화되고 있다. 교면포장에서 문제가 발생한 현장의 모습을 나타내면 Fig. 3과 같다. 따라서 장기간 공용으로 인하여 노후화된 콘크리트계 교면포장에 대하여 성능 유지(Preservation) 및 복구(Restoration)에 필요한 예방적 유지보수를 통하여 교면포장의 파손 방지 및 미끄럼 저항성을 확보할 필요가 있다.
2.3 국내·외 예방적 유지보수 공법 사례
2.3.1 국내
국내의 경우 2000년대 후반부터 예방적 유지보수 공법으로 에폭시 박층포장에 대한 연구가 본격적으로 시작되었다. 현재는 Multi-Layer overlay방식을 적용한 에폭시 박층포장이 한국도로공사 기술마켓 및 국토교통부 건설신기술 플랫폼에 등재되어 사용중에 있다. 현재 국내에서 사용중인 에폭시 수지는 자외선(UV ray) 저항성을 향상시킨 에폭시 수지로서, 저탄성계수가 8.96×102 이하이고, 고인장신율이 30~70% 수준을 갖는다. 인장강도는 14 MPa 이상이며, 기존(국내 및 해외 제품) 에폭시 제품에 포함된 노닐페놀(Nonylphenols)을 포함하지 않는 친환경 수지를 사용중에 있다.
2.3.2 국외
미국의 경우, 예방적 유지보수공법으로 1990대 초반부터 에폭시 기반 균열보수재 및 박층포장을 적용 중이며, 에폭시 박층포장 기대수명은 약15년~20년으로 추정하였다(Thin Epoxy Overlay/Healer Sealer Treatments on Bridge Decks, 2016). Table 1은 미연방도로청의 통계 자료(FHWA, 2015)로써 폴리우레탄(Polyurethanes) 계열, 실러(Sealer) 계열, 주입식 에폭시계열 대비 에폭시 박층포장의 적용분야가 광범위 하고 기대수명 또한 10~15년으로 가장 긴 기대수명을 갖는다고 기재하였다(FHWA, 2015).
유럽의 덴마크에서는 약 30년 전부터 아크릴 또는 에폭시 바인더를 사용한 박층 포장을 시공하고 있으며, 평균수명을 약 15년 정도로 보고하고 있다. 독일은 Daegusa, Silikal 등 회사에서 수십 년 전부터 아크릴계 폴리머 콘크리트를 개발하여 적용하고 있다. 최근에는 영국과 미국의 BASF社 등의 회사에서도 폴리머 콘크리트용 아크릴 수지와 에폭시 수지를 개발하여 도로 및 교량의 포장에 적용하고 있다.
Table 1.
Types and characteristics of bridge surface pavement repair methods (FHWA, 2015)
3. 에폭시 박층 포장
3.1 개요
에폭시 박층포장은 Fig. 4와 같이 기존 콘크리트계 교면포장(노출콘크리트포장, LMC포장 등)을 제거하지 않고, 기존 교면포장위에 덧씌우기 방식으로 적용 가능한 공법으로서 노출 콘크리트 포장 또는 LMC 포장 표면에 발생한 균열부를 에폭시 박층포장에 사용되는 수지(에폭시)와 골재층으로 시공하여 콘크리트포장의 수명을 연장하고, 주행 편의성을 확보한 기술이다.
무엇보다 에폭시 박층 포장은 Table 2의 콘크리트 포장 덧씌우기 공법과의 경제성 비교내용을 보면, 시공비 자체는 47% 수준으로 매우 경제적이며 공용수명을 고려한 시공비를 각각 계산하여 비교해 보면, 연간 시공비가 콘크리트 포장 덧씌우기 공법의 약 63%로 이또한 매우 경제적임을 알 수 있다.
Table 2.
Economic comparison of epoxy thin layer pavement and concrete overlay pavement
Composition | Life span | Cost | Economic efficiency |
Epoxy thin layer pavement | 15 years | 119,696 won/m2 | 0.47 |
Concrete overlay pavement | 20 years | 252,984 won/m2 | 1.0 |
3.2 재료
3.2.1 에폭시 수지
에폭시 박층 포장에 사용되는 수지는 Fig. 5와 같이 기존의 사용중인 에폭시수지를 개선시킨 우레탄 변성 에폭시 수지로 된 주제(A)와 폴리아마이드계 수지로 된 경화제를 사용하고, 접착력 향상을 위해 실란계 커플링제를 적용하였다. 주제(A)의 성분은 비스페놀 A형 에폭시와 우레탄 수지가 혼합된 수지로서, 강도 및 결합력은 우수하나 탄성계수가 높고 인장 파단율이 낮아 온도 하강 시 계면응력이 높게 발생하는 기존의 일반 에폭시 수지가 갖는 단점을 보완한 수지이다. 비스페놀 A형 에폭시 수지에 연성 및 습윤환경에서 부착력이 우수한 우레탄기를 결합시켜 저온에서 에폭시 자체의 연성을 향상시키고, 기존 콘크리트포장과 에폭시 박층포장 사이의 계면응력을 최소화하였다. 아울러, Aromatic Ring을 제거하여 자외선에 대한 저항성을 향상시켰다.
수지는 ACI 548.8M-07의 에폭시 수지 품질기준인 인장강도 14 MPa 이상, 인장파단신율 30% 이상을 만족하는 고강도, 고인장, 고연성을 갖는다(ACI 548.8M-07, 2007).
에폭시 수지는 반응온도가 증가함에 따라 경화시간이 짧아지고, 점도는 증가하지만 중합속도가 빨라지는 특징이 있다. 경화 중 열이 충분하지 않으면 중합이 불완전한 네트워크가 생성되는데 이는 기계적, 화학적 및 내열성을 감소시킨다. 경화 전 후의 에폭시 특성이 중요한데, 경화 전 에폭시 바인더의 특성은 작업성, 시공성에 영향을 미치고, 낮은 점도의 에폭시는 Pre-mix type 포장, 높은 점성의 에폭시는 Broom & seed 방법에 적합하다. 에폭시 바인더의 작업시간은 혼합량, 혼합물 온도, 대기온도 등에 영향을 받으며, 대기온도가 높고, 바인더 혼합량이 많을수록 작업시간 감소하게 된다. 경화 후에는 콘크리트 교면포장 거동에 영향을 미치는데, 휨, 인장, 압축, 부착, 열팽창계수 등의 특성이 매우 중요하다. 특히 부착강도는 기존 포장면 또는 교량 바닥면의 상태(표면 손상도, 표면 거칠기, 건조상태 등)에 따라 변동성이 크다.
3.2.2 에폭시 박층 포장용 골재
에폭시 박층 포장용 골재를 선정하기 위해, Fig. 6에 나타난 바와 같이 규사, 소성보크사이트, Flint 골재(미국)에 대한 타당성 검증을 실시하였다. 마모저항성 및 경도가 높은 각진 형태의 골재를 사용하되, 미끄럼저항성 및 내마모성 향상위해 함수율 0.2% 이하의 건조골재의 사용을 기준으로 삼았다. 에폭시 수지와의 결합력 향상 및 내구성 증대를 위해 국내에서 많이 생산되는 규사 중 ACI 548.8의 박층 포장용 골재의 입도기준과 품질기준을 만족하는 골재를 개발하였다.
3.3 실험
3.3.1 에폭시 수지(경화 전)
에폭시 박층 포장의 성능 확인하기 위해, 경화 전 에폭시 바인더를 ACI 548.8-19(2019), ASTM D2556-14(2018), ASTM C881/C881M-20a(2020)에 의거하여 실험을 수행하였다. 가사시간(gel-time) 시험은 정해진 비율로 에폭시 수지와 경화제를 1분간 교반한 후 60 ㎖의 양으로 실험을 수행하였다.
실험결과, Table 3과 Fig. 7에 나타난 바와 같이 가사시간은 수지와 경화제 배합비율에 따라 차이를 보이는데, 경화제 비율이 높을수록 가사시간이 단축되었고, 실험온도가 저온일수록 가사시간이 길어졌다. 또한, 5°C에서 gel 형성까지 90분 이상 소요되는 것을 확인하였다. 반대로 온도가 상승하면 가사시간은 단축되었으며, 40°C에서 10분 이하로 확인되었다. 이상의 실험결과로부터 수지-경화제 배합비율에 따라 가사시간 범위(15~45분)를 만족하는 온도는 각 배합에 따라 차이를 보였는데, 배합비율이 3 : 1 일때 실제 시공이 가능한 온도범위가 10~35°C로 가장 넓은 것을 확인하였다. 에폭시 박층포장시 골재와 에폭시의 부착성능을 확보하기 위해서는 골재살포 시간을 결정하는 에폭시의 가사시간이 중요한 요소이다.
Table 3.
Pot life depending on resin-hardener mix and temperature
Composition | Resin-hardener ratio | |||
1:1 | 2:1 | 3:1 | 4:1 | |
23°C pot life (min) | 18 | 28 | 32 | 43 |
Temperature range (°C) that satisfies the pot life | 10-25 | 10-30 | 10-35 | 20-40 |
에폭시 수지와 경화제 비율에 따른 점도 실험결과 저온일수록 점도가 높고, 고온일수록 점도가 낮게 나타난다. 23°C에서 점도는 에폭시 수지가 3,255 cP, 경화제는 350 cP를 나타냈으며, 에폭시 수지+경화제 바인더에서 수지 비율이 증가할수록 점도는 증가하여 2:1, 3:1, 4:1 배합에서 각각 1,423, 1,680, 1,967 cP를 나타냈다. 목표점도는 1,000-2,000 cP로 하였고, 이 범위를 만족하는 온도범위는 수지와 경화제 배합비율에 따라 다르게 나타났다. 수지비율의 변화에 따른 실험결과, Table 4와 Fig. 8에 나타난 바와 같이 증가하면 기준을 만족하는 온도범위가 전체적으로 상승하였다. 따라서 일정한 작업성을 확보하기 위해서는 수지 온도를 21°C이상을 유지하는 것으로 기준을 설정하였다.
Table 4.
Viscosity depending on resin-hardener formulation and temperature
Composition | Standard | Resin-hardener ratio | ||
2:1 | 3:1 | 4:1 | ||
23°C viscosity (cP) | 700~2500 | 1,423 | 1,680 | 1,967 |
Temperature range (°C) that satisfies the viscosity standard of 1000-2000 cP | - | 21-30 | 23-32 | 25-33 |
본 실험을 통하여 경화 전 에폭시 바인더의 인화점(ASTM D 3278-20, 2020)은 95 이상을 나타내 기준을 만족하는 것을 확인하였으며, Table 5에 에폭시 수지(경화전)에 대한 특성을 정리하였다.
Table 5.
Properties of epoxy resin before curing
Composition | Viscosity (cP) | Pot life (min) | Flash point (°C) |
Epoxy binder | 1,680 | 35 | 95 more |
3.3.2 에폭시 수지(경화 후)
에폭시 바인더의 특성을 ACI 548.8-19에 의거하여 실내실험을 하였다. 시험은 인장강도, 인장신률, 탄성계수, 열호환성, 쇼어경도, 흡수성 시험을 실시하였으며 결과는 Table 6과 같다.
Table 6.
Properties of epoxy resin after curing
3.3.3 에폭시 박층 포장용 골재
에폭시 박층 포장용 골재를 선정하기 위해, 규사, 소성보크사이트, Flint 골재에 대하여 실험을 실시하였다. 각 골재의 물리적 특성에 대하여 살펴보면 Flint 골재, 소성 보크사이트는 함수율과 경도, 마모율에 대하여 기준을 만족하였다. 하지만, 국내에서 대표적으로 사용되고 있는 규사는 박층 포장용 골재 특성인 경도와 마모율 기준을 만족하지 못한 것으로 확인되었다(Table 7). 박층 포장용 골재는 방수층으로 사용되는 에폭시 수지를 보호하는 마모층으로 마모성능이 가장 중요하다. 시험결과 소성 보크사이트가 가장 우수한 것으로 확인되었다.
Table 7.
Aggregate physical properties
Composition | Standard | Flint aggregate | Calcined bauxite | Quartz sand | |
Water content (%) | 0.2 미만 | 0.02 | 0.02 | 0.02 | |
Hardness (Mohs) | 6 이상 | 7 | 7 | - | |
Specific gravity (g/cm3) | Oven dry condition | - | 2.531 | 3.167 | 2.552 |
SSD | - | 2.565 | 3.243 | 2.575 | |
True Density | - | 2.622 | 3.426 | 2.614 | |
Absorption rate (%) | - | 1.369 | 0.783 | 0.929 | |
Wear rate (%)* | 20 이하 | 18.1 | 13.5 | 58.4 |
3.3.4 에폭시 박층 포장 특성
에폭시 박층포장의 성능을 검증하기 위하여, ACI 548.8-19 시험방법에 따라 주문진 표준사(0.85~0.60 mm)를 사용하여 에폭시 바인더와 골재의 혼합비율을 부피비를 기준으로 1 : 2.75로 공시체 제작하였다. 공시체 시험결과는 Table 8과 같이 강도 및 특성에서 모두 품질기준을 만족하는 것을 확인하였다.
동일한 과정으로 에폭시 혼합물을 혼합하여 공시체 제조 후 양생 3시간, 24시간 및 7일 후 공시체의 압축강도 및 휨강도 시험을 수행하였다. 실험은 먼저 콘크리트 슬래브 공시체 표면을 깨끗하게 정리하고, 에폭시 수지를 얇게 도포한 후 골재를 흩뿌리고 콘크리트 슬래브 공시체 표면을 고르게 한 후 양생하였다. 양생 후 잉여골재를 제거하고 실내 미끄럼 저항성 실험을 수행하였다. 부착강도는 슬래브 공시체 표면에 에폭시 바인더를 도포 후 각 골재를 흩뿌리고 양생이 완료된 후 잉여골재를 제거하고 부착강도 시험을 수행하였다.
Table 8.
Test results of epoxy thin layer packaging mixed with epoxy binder and Jumunjin standard sand
(1) 에폭시 박층포장의 압축강도 휨강도 시험
Fig. 9와 Fig. 10에 나타난 바와 같이 에폭시 박층포장의 압축강도는 양생 시간이 증가할수록 증가하였고, 특히 소성 보크사이트 골재에서 가장 높은 압축강도를 나타내었다. 이는 골재의 마모율과 경도 시험결과와 동일한 경향을 나타내었는데, 골재의 강도가 높을수록 박층 포장층의 압축강도가 증가하는 것을 확인할 수 있었다. Flint 골재의 경우에는 마모율과 경도는 소성 보크사이트와 유사하게 나타났지만 압축강도는 다소 낮게 측정되었다. 이것은 Flint 골재의 입형이 얇은 판 형태로 되어있기 때문으로 판단된다.
에폭시 박층 포장의 휨강도는 양생 시간이 증가할수록 증가하였는데, 소성 보크사이트 골재에서 가장 높은 휨강도를 나타내었다. 이는 압축강도 경향과 동일한 결과로서, 국내외 교면포장 재료로 사용되고 있는 LMC(라텍스 개질 콘크리트), HPC(고성능 콘크리트)의 압축강도와 휨강도를 비교했을 때 박층포장의 압축강도가 약 1.5배, 휨강도는 약 5배 높아 에폭시 박층포장 기술의 적용성이 매우 높은 것을 확인 할 수 있다.
(2) 에폭시 박층포장 부착강도
콘크리트 슬래브 공시체 표면에 에폭시 박층포장을 형성하고, 양생 후 잉여골재를 제거한 후 Fig. 11과 같이 부착강도 시험(ASTM C1583/C1583M)을 수행하였다. 24시간 양생 후 에폭시 혼합물이 부착된 콘크리트 슬래브 표면에 부착강도 시험용 몰드를 부착한 후 부착강도 시험을 수행하였다. 각 골재별 부착강도는 소성 보크사이트, Flint 골재, 규사 3호 순으로 높게 나타났으며 ACI 기준 1.7 MPa을 모두 만족하였다(Fig. 12). 골재원의 종류는 부착강도 발현에 영향이 크지 않은 것을 확인 하였으며, 부착강도는 에폭시의 강도, 모재 콘크리트의 강도 및 표면처리 상태에 더 많은 영향을 받는 것으로 판단된다.
(3) 에폭시 박층포장의 미끄럼 저항성
콘크리트 슬래브 공시체 표면에 에폭시 박층 포장층을 형성하고, 양생 후 잉여골재를 제거한 후 Fig. 13과 같이 실내 미끄럼저항성(BPN) 실험을 수행하였다. 미끄럼저항성 실험은 슬래브 공시체 표면에 에폭시 바인더를 도포하고, 각 골재를 살포한 후 양생 후에 측정하였다. 미끄럼저항성 실험결과, Fig. 14과 같이 모든 골재에서 60 BPN 이상으로 측정되었는데, 소성 보크사이트, Flint 골재는 각각 86 BPN, 78 BPN으로 우수한 미끄럼저항성을 보였다. 이는 국내 미끄럼 저항기준(최소 마찰계수 기준, 도로안전시설 설치 및 관리지침, 국토교통부)의 S1 등급(마찰력 확보가 매우 중요한 구간 위험도 3)의 77 BPN을 상회하는 값이다.
4. 결 론
본 연구는 내구성 및 부착력이 우수한 에폭시 박층포장 공법을 노후화된 콘크리트 교면포장에 적용하기 위해 실내물성 실험을 실시하였으며, 연구결과는 다음과 같다.
1. 경화 전 에폭시 바인더의 성능 실험결과 수지 - 경화제 배합비율이 3:1 일 때 가사시간 및 시공가능 온도범위는 각각 15분~45분과 10°C~35°C로 나타났다.
2. 경화 후 에폭시 바인더의 특성에 대하여 인장강도, 인장신률, 탄성계수, 열호환성, 쇼어경도, 흡수성에 대한 시험결과 품질기준 대비 우수한 성능을 갖는 것으로 나타났다.
3. 에폭시 박층 포장용 골재의 물리적 특성 결과 Flint 골재, 소성 보크사이트는 함수율과 경도, 마모율에 대하여 기준을 만족하였으나, 국내에서 대표적으로 사용중인 규사는 박층 포장용 골재 특성인 경도와 마모율 기준을 만족하지 못하였다.
4. 에폭시 박층 포장 혼합물의 강도 특성 및 미끄럼 저항성을 확인하기 위해 실시한 실내 물성시험 결과, 소성 보크사이트 골재를 사용한 에폭시 박층 포장 혼합물이 압축강도와 휨강도, 부착강도, 미끄럼 저항성에서 Flint 골재와 규사를 사용한 혼합물에 비해 가장 우수한 결과가 나타났다.
결과를 종합해 보면 노후 콘크리트 교면포장(노출, LMC 등)에 대한 예방적 유지보수공법으로 에폭시 박층 포장공법을 적용한다면 콘크리트포장에 발생한 균열부의 충전은 물론, 기존 콘크리트 포장부를 제거하지 않으면서, 상면에 두께 약 3~6 mm 전후의 박층 에폭시 포장층을 시공하여, 콘크리트 포장부의 열화를 방지하고, 포장층과 구조물(바닥슬래브)의 내구수명을 향상시킬 수 있을 것이다. 이를 통해 경제적이고 합리적인 콘크리트계열 교면 포장의 예방적 유지관리가 가능해질 것으로 판단된다.