1. Introduction
2. Asphalt mixture
2.1 Aggregate inspection
2.2 Asphalt inspection
2.3 Mix inspection
2.4 Mix temperature
2.5 Mix delivery
2.6 Mix defects and appearance
3. Preparation of surface
3.1 Subgrade
3.2 Base course
3.3 Prime coats and tack coats
4. Weather
5. Placement
5.1 Pavers
5.2 Depth checks
5.3 Inspection of mat
6. Compaction/density
7. Sampling at site
8. Payment factor/incentives
9. Communications and responsibilities
9.1 Truck driver
9.2 Dump person
9.3 Paving crew
9.4 Roller operator
10. Conclusions
1. Introduction
Construction of a new pavement is required to satisfy the design criteria and need to provide maximum service period with less maintenance. The objective can be achieved by paying detail attention at each step during the construction of pavement. Quality control primarily involves all the procedures initiated from contractor’s part (Burati et al., 2003; Shekharan et al., 2007). Quality control of new asphalt pavement construction involves the frequent monitoring of the processes that include selection of aggregate, selection of asphalt content, proper mix design, laying and compaction and meeting the design requirement and specification (Petkevičius and Sivi1evičius, 2008; Bubshait, 2001; Wu et al., 2017; Mayakaduwa, 2011; Benson, 1999). Any deficiencies in quality control at any step can lead to a poor performance pavement (Shekharan et al., 2007; Minchin et al., 2008; Akkinepally and Attoh-Okine, 2006; Suh et al., 2009; Schmitt et al., 1998). Hence, it is important to monitor all the construction quality control index for building a new pavement. In a quality control index first process involves the sorting out of materials like how it will be manufactured, transported, placed, hauled and its viability to meet all the design requirements and specifications for the mix design. The second process involves the contractor submits the proposed mix design based on the specification and selected materials that are determined to yield good performance and achieve the design specification for the project. The design will be then produced and tested to assess its performance and based on the evaluation of the mix either approval or revision is suggested by the evaluator. Once the mix approved, plant mix is prepared for constructing the new pavement. In the final process hauling, paving, and compaction of the pavement take place. Throughout the whole process the quality control of construction needs to be maintained in order to have a strong and low maintenance pavement. Fig. 1 shows the process of the quality management of a new asphalt concrete pavement.
The paper presents an extensive insight of the quality control index that need to be followed while constructing a new asphalt pavement. It provides quality control index at each step of the construction process which are: aggregates, asphalt, mix design, placing of material, compaction and individual responsibilities at different stages.
2. Asphalt mixture
In general asphalt mixture consists of asphalt and aggregate. Asphalt pavement can be made with different types of asphalts and aggregates. Typical asphalt pavement are asphalt concrete, open-graded asphalt friction course, sand asphalt hot-mix, sheet asphalt hot-mix and emulsified asphalt mixes (Schmitt et al., 1998; Cominsky et al., 1994; Benson, 1999). Among all these mixes asphalt concrete is considered as the highest quality type of asphalt pavement. Aggregate with well graded properties is blended and heated with optimum quantity of asphalt cement together in order to make the hot mixture at a hot-mix plant. Properly coated aggregate with asphalt cement is hauled to the construction site where paver is used to spread it on the prepared roadbed. Then the roller is used to compact it into a final pavement before the hot mix asphalt cools down. Asphalt and aggregate are mixed together in a central plant which is known as plant-mixed bituminous. The proper procedure needs to be followed for ensuring the high quality product. The mixing plants are mainly divided into two categories: batch plant and dryer-drum plants.
Batch plant consists of cold-feed system, asphalt cement supply system, aggregate dryer, mixing tower and emission control system whereas drum plant major components are cold-feed system, asphalt cement supply system, drum mixer, storage silos, and emission-control system. The following basic quality control measures need to be taken in order to have quality product (Hall and Williams, 2002; Cominsky et al., 1998; Pathomvanich, 2000; Battikha, 2003; Quality Control Manual for Hot Mix Asphalt for the Quality Control Quality Assurance Process, 2009; Xu and Chang, 2016).
-Gradations of cold feed or stockpile
-In batch plant hot-bin gradations
-Adjustments of cold-feed
-In batch plants adjustments of hot-bin weight
-Ensuring proper binder content
-The gradation of aggregate in mixture
-The adjustments of mixing time and temperature
-The various test records for checking properties such as volumetrics or strength test need to be continuously monitored
-While preparing the mixture design in plant additional care needs to be taken for aggregate, asphalt and mix design itself.
2.1 Aggregate inspection
1. Good stocking procedure for aggregates is vital to have quality asphalt mixture. Poor stockpiling segregates the aggregate particles whereas good stockpiling retains the proper gradation. The best procedure of stockpiling aggregates is to build the stockpile in layers with a range of different-sized particles. Stockpiling of aggregates should be built on a clean, dry and stable foundation with proper drainage in horizontal or gently sloping layers. Trucks and front-end loaders travel on stockpiles should be minimized in order to prevent breakage and generation of fine aggregates.
2. After meeting the requirement of cost and availability, the aggregates should have cleanliness, toughness, proper shape, size and gradation, surface texture, absorptive capacity and affinity for asphalt.
3. The materials which are segregated should be blended by the loader before introduction to the cold feed bins and trucks.
4. Bulkheads need to be in cold feed bins so that aggregate cannot overflow to the adjoining bin. To remove the oversized materials scalping screen should be placed. Cold-feed bins should be calibrated.
2.2 Asphalt inspection
While carrying asphalt in trucks and railroad cars, it is important to make sure to check the previously carried petroleum products on that truck or non-asphaltic residue carrying in lieu with asphalt, contaminating the asphalt cargo. Table 1 illustrates the information that might be followed before loading of asphalt.
Table 1.
Guide for loading asphalt products (Principles of Construction of Quality Hot Mix Asphalt Pavements, 1982)
2.3 Mix inspection
During design, production and placement, asphalt mixture should have important properties such as stability, durability, flexibility, fatigue resistance, skid resistance, permeability, workability, asphalt binder content and air voids (Abu Abdo et al., 2010; Li et al., 1997; Wegman, 1996; Abu Abdo et al., 2010). Table 2 presents the information of effects of improper mixture.
Table 2.
Causes and effects of improper asphalt mixture (Hot Mix Asphalt Paving)
2.4 Mix temperature
The temperature of the mix is one of the most vital part in controlling the quality. If the mix is too hot then blue smoke can be detected from the mix. Along with that the presence of smoky load also represent the use of fuel oil as an anti-adhesive in the truck bed or cargo. Typically the temperature of the mix should not exceed 325°F (163°C). On the other side if the temperature is too low then mix may appear sluggish and show a non-uniform distribution of asphalt (Ksaibati and Butts, 2003; Thurner, 2001; Standard Specifications for Highway Construction, 2008). Also, the abnormal high peak in the truck bed indicates that the mixture is underheating and has low asphalt content. It is important to note that the temperature of the aggregate control the temperature of the mix. As a result, if the aggregate is overheated it may make the mixture harden whereas underheating may cause problem to coat with asphalt.
2.5 Mix delivery
Mix is delivered to the paving site in trucks. Hauling trucks vary by size and type. The uniformity of equipment is very important in hot-mix paving operation. Careful observations should be made while determining the quantity of asphalt mix delivered from plant to paving site. The accuracy of truck scale needs to be monitored periodically.
2.6 Mix defects and appearance
Mix defects are observed at its best when the temperature is checked or truck bed raised. Some indications of these deficiencies provide briefly to maintain the quality control of the mix.
2.6.1 Stiff appearance
The mix can become stiff if load has an unusual peak, too cool or below the optimum placing temperature. It is important that mix should be similar color throughout the load. Improper mix in the plant can show some parts of the mix being lighter in color than others.
2.6.2 Mix slumped in truck
If the material in the truck lies flat or nearly flat it is either due to the excessive asphalt content in the mix or excessive moisture. In general the deficiencies appear as excessive shininess on the mat surface.
2.6.3 Lean and dull appearance
The mix with too low asphalt content can be appeared as dry, granular, improper coated, and a lack of typical shiny black lustre. It can be detected either by its appearance or by unsatisfactory compaction under roller. It is important to note that excess fine aggregate in the mix can also present the same look. However, it can be distinguished by the mix texture and by watching for shifting of the mix under the roller.
2.6.4 Rising steam
Steam rising can be seen when asphalt mix is dumped into the hopper of the paver due to excess moisture. It may appeare as bubbling and popping and looks like boiling.
2.6.5 Segregation
Segregation generally occurs due to the improper handling of aggregates. It is the most common problem. The coarse aggregate tends to roll out of the truck at the very beginning or end of the load while placing into the paver.
2.6.6 Contamination and bleeding
Mixes can be contaminated due to the foreign substances such as spilled gasoline, kerosene, paper, trash and dirt. It is recommended to use non-petroleum based agents for spraying the bed of trucks. Precautions should be taken while using diesel fuel as excess of it can be absorbed by the mix and may create fat spot. It may also leach the asphalt from the mix with it. Contaminated load should be rejected, removed and replaced.
3. Preparation of surface
In general preparation of surface is required in three cases:
1. On newly constructed subgrade, aggregate base or HMA base courses
2. Over existing pavements
3. Widening contracts, combination of existing pavement and a base course
Overall surface preparation includes the observation of all surfaces are clean and free of loose debris and dust, prime or tack coat properly applied, paint removal prior to overlay, localized failures removed and replaced, milling is smooth to desired grade without scabs and if any sealing required for cracks. Only construction of new asphalt pavement is discussed.
3.1 Subgrade
A subgrade should have proper moisture content, density, structural support and smoothness to support the paving operation (Pratico, 2007; Patel et al., 1997). Following quality control needs to be maintained while preparing the subgrade for paving:
1.Subgrade should be free from soil that is too weak to properly support the paving equipment. It should maintain the design dimensions and construction should not be permitted on distorted subbase or subgrade until it fixed.
2.Proofrolling can be used to inspect the compaction and suitability of the subgrade before receiving HMA base.
3.The number of trucks and their limits should be noted. If excessive distortions are observed under the truck then steps should be taken to dry it up or stabilized.
4.Transverse and longitudinal grade control should be maintained carefully. Grade can be adjusted by removing or adding material if it is not under tolerance limit.
5.In case of full depth pavement the subgrade should be firm, hard, unyielding and free from loose particles and accumulations of dust.
6.Use of prime cost for substituting proper preparation of subgrade soil is not recommended.
3.2 Base course
After finishing the construction of stable subgrade, the base course should be placed on it with quality base material. The quality base material should meet all the requirements related to moisture content, density, structural strength and smoothness. The implementation of prime coat or new asphalt mix is permitted ensuring that the base is stable, dry and no defection observed on the surface.
3.3 Prime coats and tack coats
In general the application of prime coat has three advantages:
1.It prevents the occurrence of slip plane developing between the base and surface course.
2.During traffic it prevents the base material from shifting before the surface course is placed.
3.It protects base course against wet weather. It acts as a temporary waterproofing layer which can absorb excess moisture during rain before paving.
It is recommended to provide prime coat with a pressure distributor to the base course at least 48 hours before the start time of paving. It is important to note that 24 hours are recommended to absorb the prime coat material by the base course. If excess prime coat material remains and it is not absorbed then excess material should not be blotted with sand or removed. In general the application rate for medium curing cutback asphalt (MC-30, 40 or 250) in between 0.2 to 0.5 gallons and emulsified asphalt (SS-1, SS-1 CSS-1) the range vary between 0.1 to 0.3 gallons per square yard. However, it is the project engineer who decides the proper application rate based on the conditions.
Tack coat is a form of bituminous emulsion placed between two bituminous layers, so that the two layers can act as a single monolithic unit to sustain the traffic loads. In general four types of tack coat materials are used for increasing the interlayer bonding strength are:
3.3.1 Hot asphalt cement
Hot asphalt cement is black or dark-colored natural or manufactured cementitious substances which can be solid, semisolid or viscous and composed high molecular weight of hydrocarbons. PG 64-22, PG 76-22, PG 76-22M and PG 58-28 common binder type which are often used as tack coat material (West et al., 2005).
3.3.2 Asphalt emulsion
Asphalt emulsion consists of asphalt, water and small amount of emulsifying agent. It is most widely used because of its uniformity, energy saving and safer application than asphalt binder and cutback asphalt. Asphalt emulsion is categorized into three categories which are anionic, cationic, and nonionic. RS, MS, SS, QS, SS-1, SS-1h, CSS-1, and CSS-1h are most common types of emulsions (Paul and Scherocman, 1998; Cross and Shrestha, 2004).
3.3.3 Asphalt cutbacks
Asphalt cutback consists of asphalt binder and petroleum distillates. However, recently the use of cutback asphalt as a tack coat is decreasing because of its use of volatile chemicals which is harmful to the environment (Mohammad et al., 2012; Roberts et al., 1991). Cutbacks are divided into four categories: Rapid curing (RC-70, RC-250, RC-800, RC-3000), medium curing (MC-30, MC-70, MC-250, MC-800, MC-3000) and slow curing ( SC-70, SC-250, SC-800, SC-3000) (Ghaly et al., 2014; Du, 2011; Al-Qadi et al., 2008).
3.3.4 Trackless tack coat
Trackless tack coat comprises of polymer modifier and hard base asphalt which helps to reduce the tracking problem. It has higher shear strength compared to the traditional tack coat like CRS-1 and SS-1 (Clark et al., 2012; Mohammad et al., 2011; Raposeiras et al., 2013; Hakimzadeh et al., 2012). Although due to its high brittleness and low top down cracking resistance it might exhibit vulnerable in cold region (Chen, 2009; Ziari and Khabiri, 2007; Leng et al., 2008; Chen et al., 2012).
Quality control factors for tack coat materials are following:
a. Asphalt distributor
b. Clogged nozzles
c. Nozzle size
d. Nozzle orientation
e. Distribution bar pressure and speed
f. Spray bar height
g. Calibration of distributor
h. Maintaining consistent temperature
i. Tracking due to haul trucks
j. Tack coat coverage
k. Tack coat application rate
4. Weather
Weather is an important factor for the new HMA construction. Air and surface temperatures play an important role in determining the paving operation decision. If both air and surface have low temperature the mix cool too quickly. Mixture should not be laid on wet surfaces even if the air and surface temperatures are within limits. During rainy weather good communication should be maintained between mixing plant and paving site. Following condition can happen at the job site and the engineer may follow the procedure to maintain the quality control.
1.If there is too much rain then the mix should not place and return the haul truck to mixing plant. In this case material can be recycled later. The cost associated with that is hauling the truck back to the plant and reprocessing the material in plant.
2.If the rain is relatively light and appeared to be likely continued for some time, paving may continue ensuring that there is no puddled water and pavement surface is properly tacked. However, paving should not be continued if there is puddled of water.
3.Although some specifications might allow to use in transit mix to use. The problem is that in this case the mix cool very quickly due to low temperature and the condition makes it difficult to get desired density. High air void content leads to poor performance of the pavement.
4.Another way is to store the mix in the haul truck until rain stops. However, care must be taken as on that duration mix might lose temperature. In general 2-3 hours hauling time in the truck causes little harm to the mix. Table 3 presents the basic guidelines on weather check during paving operation.
Table 3.
Basic guidelines on weather check during paving operation (Hot Mix Asphalt Paving)
5. Placement
Placement of asphalt mixture consists of several steps such as mixture pick up with trucks from plants, unloading, and placement with paver (Miller et al., 2011).
Haul trucks pick up the mixture from the plant and deliver it to the job site at the correct temperature with appropriate quantity. There are three main types of haul trucks used which are:
End-dump truck is the most common maneuverable type of truck used in the field either tractor-trailer configurations or straight-frame trucks. However, this kind of truck is most prone to thermal and material segregation. It has rear-hinged and hydraulically-lifted dump box which helps to release the mixture into hopper. They have less hauling capacity compared to other truck types and hence not idea for large project. Belly-dump truck is a tractor-trailer unit and it is less maneuverable due to its unit. However, it has higher hauling capacity than end dumps. Flow-boy can be either tractor-trailer or straight-frame truck. The capacity and maneuverability depend on its configuration. Following quality control measurement should be made while operating trucks:
1.The gates must be tight otherwise truck bed prone to leak mix. Also, check for hydraulic and fuel leaks.
2.Ensuring that there is no foreign materials in the mix. Truck bed should be inspected before putting the mix on the bed.
3.Trucks should be equipped with traps and capable of keeping the material from cooling or becoming contaminated.
4.Watertight traps need to be overlapped with the bed of trucks so that it can prevent rain and foreign material getting into the mix. Before placing mix, traps should be rolled back to inspect the appearance of the mix.
Other than truck pick up machine or window elevator also are used to deliver the mix. It simply picks up the material and delivers to paver. Some of the pick-up machines have the ability to reduce thermal and material segregation by mixing the material by putting it in the hopper. Material transfer vehicle (MTV) is another alternative, only the difference with other equipment is that it has built-in drive system. It has internal storage capacity and help to deliver the mix to paver if haul truck is not immediately available. It is important that before using MTV, load carrying capacity of the road should be checked due to its heavy weight.
5.1 Pavers
Pavers are self-propelled asphalt laydown machines which consist of following process: load the mixture in the front, carried to the rear by conveyors, spread out by augers and leveled and compacted by a screed (Miller et al., 2011; Ebrahim Abu El-Maaty et al., 2016). It consists of two main components which are tractor unit and the screed. The mixture laid by paver is known as lift or course.
Tractor unit consists of hopper, salt conveyors, and augers. It is the material feed system that pulls the screed (MNDOT Bituminous Manual, Application of Quality Assurance Specifications for Asphalt Concrete Mixtures, 2006). The kick back paddles of the auger need to maintain properly otherwise the area around the gear box of auger can be a source of segregation. On the other the hand screed takes the head of material from augers, strikes it off at correct thickness and gives the mat its initial compaction. This component has the greatest effect on the final cross slope, smoothness and appearance of mat.
Pavers are three types: wheeled paver which has two long drive wheels, track paver is driven by the track system instead of wheels and spray paver which sprays tack and applies asphalt mix seconds later. Several factors influence the performance of paver such as paving speed, head of material, mix consistency, pre-compaction, and screed angle of attack which impacts the vertical position of the screed. If any of these mentioned factor have deficiency then desired performance in mat density, depth and texture will not be achieved. The quality control checks for the paver are following:
1.Vertical position of free-floating screed of paver mainly depends on three major factors: a) angle of attack, b) head of material, and c) paving speed.
2.Paving speed needs to be adjusted to give a uniform texture and coordinate with plant production.
3.Prevention of bumping the paver by truck. It can cause transverse marks and ridges on the finished mat.
4.Prevention of truck driver holding brakes. It can cause the increase of mat depth and paver wheels to slip or break traction which create a non-uniform edge line and bump in the mat.
5.Paver engine should be in good operating condition. The faulty power and speed surges can cause ripples, waves, or auger shadows in the mat.
6.Paver tires should be equal and over inflation free. Unequal and over inflation can cause rough and uneven mat.
7.Prevention of loose or uneven tensioned traction drive chains. It may cause power or speed surges which may result in ripples, waves or auger shadows in the mat.
8.It is also important that after paving a short distance, the mat needs to be checked on following issues: a) proper width, b) proper elevation, c) proper slope, d) inner edger plate, e) flow of material.
5.2 Depth checks
The thickness of the uncompacted mat should be checked immediately behind the paver. In general uncompacted mat should be placed with approximately ¼ inch additional thickness per inch of depth placed. Too thick or too thin mat does not compact properly. Too thin mat drags the mix aggregate whereas too thick mat difficult to compact to the required density. Along with that proper grade and cross slope should be inspected at various point across the lane.
5.3 Inspection of mat
In general mat problem arise in asphalt mixture during or soon after the laydown or compaction operations. The problems may occur due to two main reasons which are: equipment and mixture. Quality control of mat can be ensured by inspecting the issues on laying mat which are:
1.Temperature of the mix
2.Pavement surface appearance (Surface texture, tearing or scuffing, texture irregularities, surface smoothness, lack of uniformity, improper aggregate gradation)
3.Pavement crown
4.Pavement geometrics
5.Joints in between adjacent mat (transverse and longitudinal)
Fig. 2 presents the quality check for the finished mat.
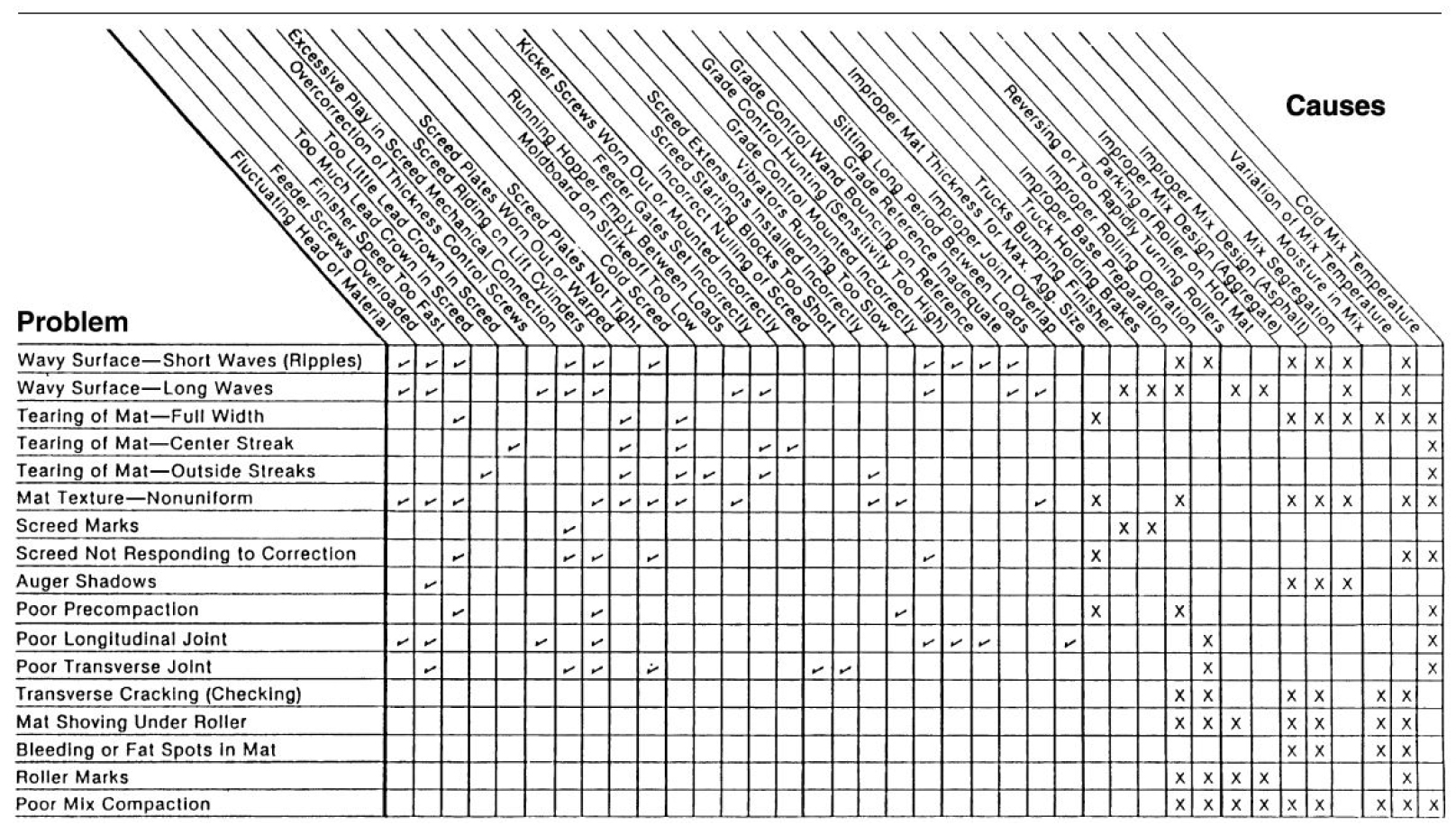
Fig. 2
Mat problems and their causes (check indicates causes related to the paver and x presents other problems) (HMA paving Field Inspection)
6. Compaction/density
Compaction is the most vital factor in the construction of a HMA pavement. It increases the fatigue life of mixture and decreases rutting, oxidation/aging, moisture damage, low temperature cracking (Yiqiu et al., 2014; Welborn, 1984; Xu and Chang, 2016; Horan et al., 2012; Liu et al., 2016; Yiqiu et al., 2014). If the pavement has not been compacted to the proper density it will not ensure strength and stability even if it has desirable mix design characteristics. Compaction starts after the mixture has been placed on the roadway. There are different types of compaction equipment including: static steel wheel rollers, pneumatic tired rollers and vibratory steel wheel rollers (Ameri et al., 2014; Ohrn and Schexnayder, 1998; Zambrano et al., 2006; Horan et al., 2012; Horan et al., 2012; Liu et al., 2016)
Vibratory double steel drum roller consists of a steel drum at the front and rear of the vehicle. It can operate either in vibratory or static mode and apply dynamic load for greater compaction (Asphalt Pavement Inspector’s Manual, 2003). Pneumatic tired roller or rubber tired roller have multiple smooth tires on each axle and operate with static compressive force that kneads the mixture together. Following cautions need to be addressed before compaction:
1.Rollers should be checked on the basis of its total weight, weight per inch of width (steel-wheeled rollers) and average ground contact pressure (pneumatic-tired rollers).
2.Rollers need to have a sprinkler system to wet the drums or tires to prevent it from sticking with mat materials.
3.It is recommended to be equipped with drip pans in order to prevent oil, grease or fuel from dropping onto the roadway.
4.Tire should be warmed up and uniform tire pressure is essential. For pneumatic tired rollers adjustment of the tire pressure should be done based on thickness and underlying support.
5.Clutches are required to function smoothly and any jerks from roller starting, stopping and reversing should be avoided.
Rolling operations are also important in order to ensure a proper compaction. In general there are three types of rolling operations: initial (breakdown) rolling, intermediate rolling and finish rolling (HMA paving Field Inspection, Decker, 1996). Initial rolling is the first pass on the freshly placed mat. It is recommended to start the rolling operation on the low side of the mat and progress toward the high side. It is due to the mixtures tendency to migrate toward the low side of the mat. Intermediate rolling is all the subsequent pass by the roller in between start and finish before the mix cools to 185°F (85°C). It should be continued until all the mix compacted thoroughly by following the same manner as breakdown rolling. Finish rolling has been done in order to provide surface improvement by removing the roller marks. The basic sequence for thin lift (a lift of less than 2 inch) are: a) transverse joints, b) outside edge, c) initial or breakdown rolling, d) intermediate rolling and e) finish rolling. The basic sequence for thick lift (a lift of 4 inch or more) is: a) transverse joints, b) initial or breakdown rolling, c) outside edge, d) intermediate rolling and e) finish rolling. The speed of the roller and its pattern or coverage should be monitored to ensure that the same amount of compaction has been applied at all points transversely across the lane. In general for static wheel and pneumatic tire rollers in the breakdown position the maximum speed should not exceed 4 km/h. For a vibratory roller the maximum speed is recommended 6 km/h. The vibratory frequency is important in order to get adequate density and layer smoothness. The vibratory impacts of 30 to 40 per meter (10 to 12 per foot) are needed. Breakdown and intermediate rollers should be operated close to paver as possible to obtain density to a minimum temperature of 80°C. More rollers should be used if rollers cannot keep up with the speed of paver. Upon completion of the mat three important criteria should be checked: a) surface texture, b) surface tolerance/smoothness, and c) density. Table 4 presents the factors that influence the compaction process.
Table 4.
Factors that effected the compaction process (Principles of Construction of Quality Hot Mix Asphalt Pavements)
7. Sampling at site
Quality control of HMA pavement construction or its required achievement can be checked by sampling at site or experimenting the sample in lab (Chang and Hsie, 1995; Kim et al., 2010; Tsai and Monismith, 2009; Tsai and Monismith, 2009). In general quality control of HMA is based on testing of aggregates for quality, temperature of mixture, binder content, density and smoothness. In terms of mixture the acceptance criterial of HMA depends on air voids and binder content whereas SMA mixtures depend on binder content and gradation. Contractor is responsible for conducting the onsite testing. Testing of sample at site (destructive or non-destructive) and laboratory should be conducted according to the highway agency prescribed specifications (Lin et al., 2016). Several types of samples should be obtained at different stage of the project in order to maintain the quality of the pavement construction. Such tests are:
1. Plate samples
2. Truck samples
3. Core samples
4. Appeal samples
Before obtaining the sample, it is important to determine where to take the sample and process should be random so that there is no bias in obtaining the sample. In general the smoothness of the pavement is measured using 10-foot straight edge and inertial profiler (Hearne Jr et al., 1996; Karamihas, 2003; Stroup-Gardiner et al., 2005; Wagner, 2003; Smith et al., 2002).
8. Payment factor/incentives
Quality control of the asphalt pavement depends on many variables such as material properties, smoothness, compaction and so on. Many highway agencies incorporate payment factor clauses in their construction to encourage excellent quality pavement and at the same time failing to assess the required quality can reduce the payment as well (Shuler et al., 2007; Deacon et al., 1997; Gedafa et al., 2010; Hughes et al., 2011). Also, some agencies award incentive payments above or beyond the contract price for superior quality. Pay adjustments for bonuses and penalties can be determined by the highway agencies (Shuler et al., 2007; Gedafa et al., 2010). It can be in areas such as mixture, aggregates, surface preparation, materials including tack coat, placement, equipment, labor, tools, compaction (air voids), and so on.
9. Communications and responsibilities
All the participant in the project should maintain professional, agreeable, and cooperative attitude to each other. Tact or proper decorum should be maintained throughout the project. Owner or personnel behalf of owner should work together with contractor to make worksite environment productive rather than delaying the progress (Hot Mix Asphalt Paving). Following basic conundrum should be made at the worksite.
1.Don’t pre-judge the contractor and let the personal differences or personal opinions interfere with working relationship. It is a good practice to start with a premise that contractor is fair minded and intends to do their job productively.
2.It is not recommended to avoid onsite criticism of the contractor and such incidence is unwarranted and hurt working relationships.
3.Courteous and respectful behavior always bring up a good relations which is beneficial all concerned.
4.It is important from the owner’s point of view not to get involved in the contractor’s labor relations. It is contractor’s responsibility to deal with it.
In order to maintain quality control of asphalt pavement, each personnel need to be well aware of their assigned responsibilities. There are several responsible personnel based on their duty: truck driver, dump person, paving crew (paving operator, screed operator and lute person), roller operator (breakdown and intermediate and finish roller). Good quality control can be hampered by any of the responsible personnel’s fault. Below are the recommended responsibilities suggested for each responsible personnel:
9.1 Truck driver
1.Truck should be loaded with multi drop procedures and trap load so that maximum temperatures can be maintained.
2.Safe proceedings to the paving site with lining up properly in front of the paver.
3.Transfer the material into the transfer unit without making bump.
4.After making the contact with the paver, release the tailgate and discharge the mixture in a mass. While discharging the mass the bed of the truck should be continued to raise.
5.Another procedure can be followed before opening the tailgate by raising the bed first. Set the discharge position of the truck by stopping short of the paver by 1-2 inches and raise the bed until the load shift to the rear. The paver operator will start moving the paver forward after observing the shifting of material. At the end, ensuring the detection of forward motion of the paver the truck driver continued to raise the bed to allow the discharge of mass.
6.When the loading is finished, exit immediately.
9.2 Dump person
1.Dump personnel generally responsible for safely directing the truck to correct position in order to discharge the material in the hopper. It is his or her responsibility to warn paving crew about surrounding obstructions such as overhead or when dangerous situations arise.
2.The coordination between truck and paver so that discharge can be made without bumping the paver.
3.It is recommended watchful eye should be maintained by the dump personnel so that hopper have at least 25% full at all times.
9.3 Paving crew
Paving crew consists of paver operators, screed operator and lute person.
9.3.1 Paver operators
1.Balanced paving speed in order to have balance delivery with proper paver capacity and compaction.
2.Keeping the head of material of screed operator within a plus or minus one inch tolerance.
3.It is recommended to steering and holding the paver to a pre-determined reference.
4.Ensuring smooth starting and stopping operation in order to prevent end of load roughness.
5.Working with the dump personnel to make sure the truck does not bump the paver and hopper have at least 25% materials at all times.
9.3.2 Screed operator
1.The screed personnel is responsible for setting up screed and help to implement the required width, crown, slope and depth by the specifications.
2.The proper heating of screed and maintaining the coordination with paver to keep the head of material within plus or minus one inch tolerance.
3.Maintaining screed adjustments in order to produce a textured mat and ensuring the mat being placed by using established references.
4.Following the proper procedure for constructing sound transverse and longitudinal joint.
9.3.3 Lute person
1. Lute personnel is responsible to assure that mat is deficiency free before compaction.
2. Any place where paver cannot be used, hand work should be done by lute person.
3. Repairing the imperfections of mat and cleaning the paver at the end of the shift.
4. Preparing the transverse and longitudinal joint and end of pass wedges or tapers before compaction.
9.4 Roller operator
9.4.1 Breakdown and intermediate roller operator
1.Operators are responsible for obtaining required compaction when HMA is under proper temperature range without damaging the aggregates. Roller personnel should maintain communication with paving crew and foreman before the arrival of HMA.
2.Carefully check the water system and determine the lift thickness. Checking of water system is very important to avoid material pick-up and also try eliminate excessive usage of water.
3.Careful about the material temperature delivered to the paver and determination of rolling drum mode (static or vibratory) based on the required density.
4.Determination of suitable rolling speed and coverage in order to achieve desired compaction and smoothness. Rolling pattern need to be established and adjusted for paving width, roller drum width, unsupported edges, and drum overlap.
5.Careful monitoring of rolling temperature and working with the optimum temperature zones.
6.It is important to note that good compaction can be ensured by maintaining consistency throughout the entire working shift.
9.4.2 Finish roller
1.Operator are generally responsible for removing all surface marks, blemishes and in some instances may be worked for getting final compaction if desired density have not achieved by the breakdown and intermediate roller.
2.Proper communication and coordination with the paving crew, foreman, breakdown operator and quality control personnel needs to be maintained.
3.Careful inspections need to be made on determination of rolling mode, material temperature and avoiding tender zone, water system and usage, rolling pattern and coverage, rolling temperature and working within the optimum temperature zones and at last maintaining consistency throughout the entire shift.
10. Conclusions
This paper deals with the quality control management of new asphalt concrete pavement construction. Details of quality control related to each stage of construction process were documented, and problems were reported when the process was defective. Following main points can be drawn:
∙Proper storage procedures for aggregate are essential to have a quality asphalt mixture to avoid segregation. When transporting asphalt on trucks and railroad cars, need to identify the previously carried products on that truck or non-asphaltic residue carrying in lieu with asphalt, which can contaminate the asphalt cargo. Mix design should include stability, durability, flexibility, fatigue resistance, skid resistance, permeability, workability, asphalt binder content and air voids
∙Subgrade should not have fragile soils that are too weak to properly support the paving equipment. Air and surface temperatures play an important role in determining the paving operation decision.
∙Careful monitoring should be maintained while operating the paving equipment (haul trucks, paver and rollers). Mat evaluation should be made according to the mix temperature, the surface appearance, the pavement crown and its geometry.
∙For proper compaction, roller speed, coverage and pattern must be monitored.
∙Onsite sampling and payment incentives are considered an effective way to ensure quality control at each site of the construction process.
∙Communications between project participants and successful completion of responsibilities are essential to the construction of high quality pavement.